The aim was to develop a series production process for EUVL. The process consisted of assembly in the clean room, cable assembly and testing of the sensors to be glued in. The end product for EUVL must meet all needed requirements, especially the cleanliness requirements of the semiconductor industry. During the project, the complete process development for the clean room was carried out and adapted to the requirements in the EUVL area.
EUVL is a high-vacuum semiconductor technology that needs extremely high cleanliness. This is necessary because the smallest impurities in the high vacuum can have devastating consequences for the quality of the components. Processes such as gluing for high vacuum, pressing and welding are relevant for the production of the component.
For gluing in the clean room, it was very important to have the right parameters and the right equipment, e.g. to select special dosing needles. For welding, the biggest challenge was to meet the high cleanliness requirements for EUVL.
The component can no longer be wet-chemically cleaned after welding. A special tooling for encapsulation during welding was developed for this purpose. Checking the cleanliness of a weld seam combined with a helium leak test in the clean room and a 20 bar pressure test presented a very big challenge. The leak test for the high-vacuum application in particular required special tooling.
The pressure test is carried out to meet the requirements for human safety. If this pressure test cannot be completed successfully, this would cause a risk to the user when using the product. The components may not be touched with hands (not even with gloves), but may only be processed with specially developed tools made of approved materials. The complexity of the process and the special requirements meant that many functions had to be mapped in the tools at the same time. The process has been fully developed and documented. The process was then introduced at the customer and the employees were trained using the work instructions.
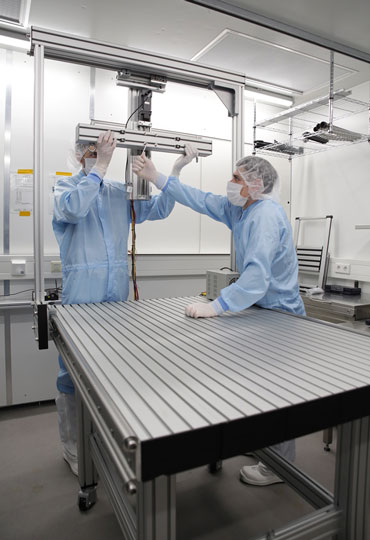
Preparation of the lifting device
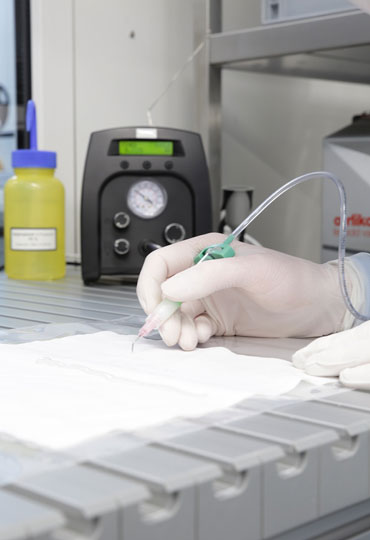
Dosing tests to determine the correct parameters when gluing
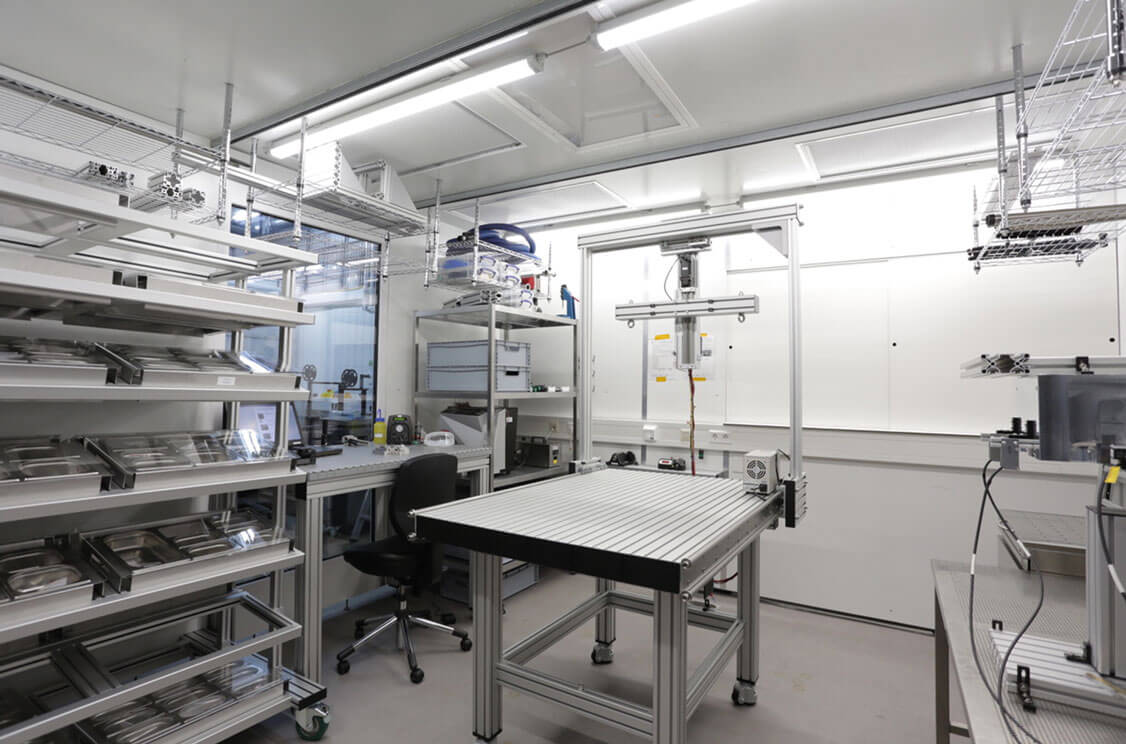
Clean room
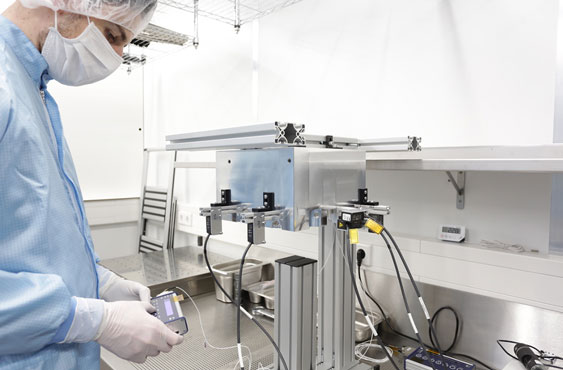
Aligning the device for positioning tests
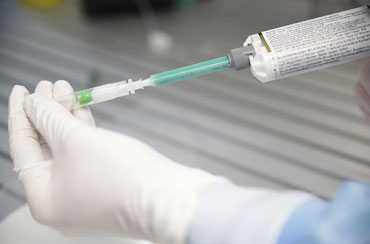
Preparation of the glue.
Application with automatic dosing system